The Science Behind Pharmaceutical Freeze Drying: Everything You Need to Know
Modern pharmaceutical manufacturing depends on providing consistent efficacy and the longest possible shelf life. Freeze drying, also known as lyophilization, is a core process for achieving these goals to provide patients with safe and effective medications.
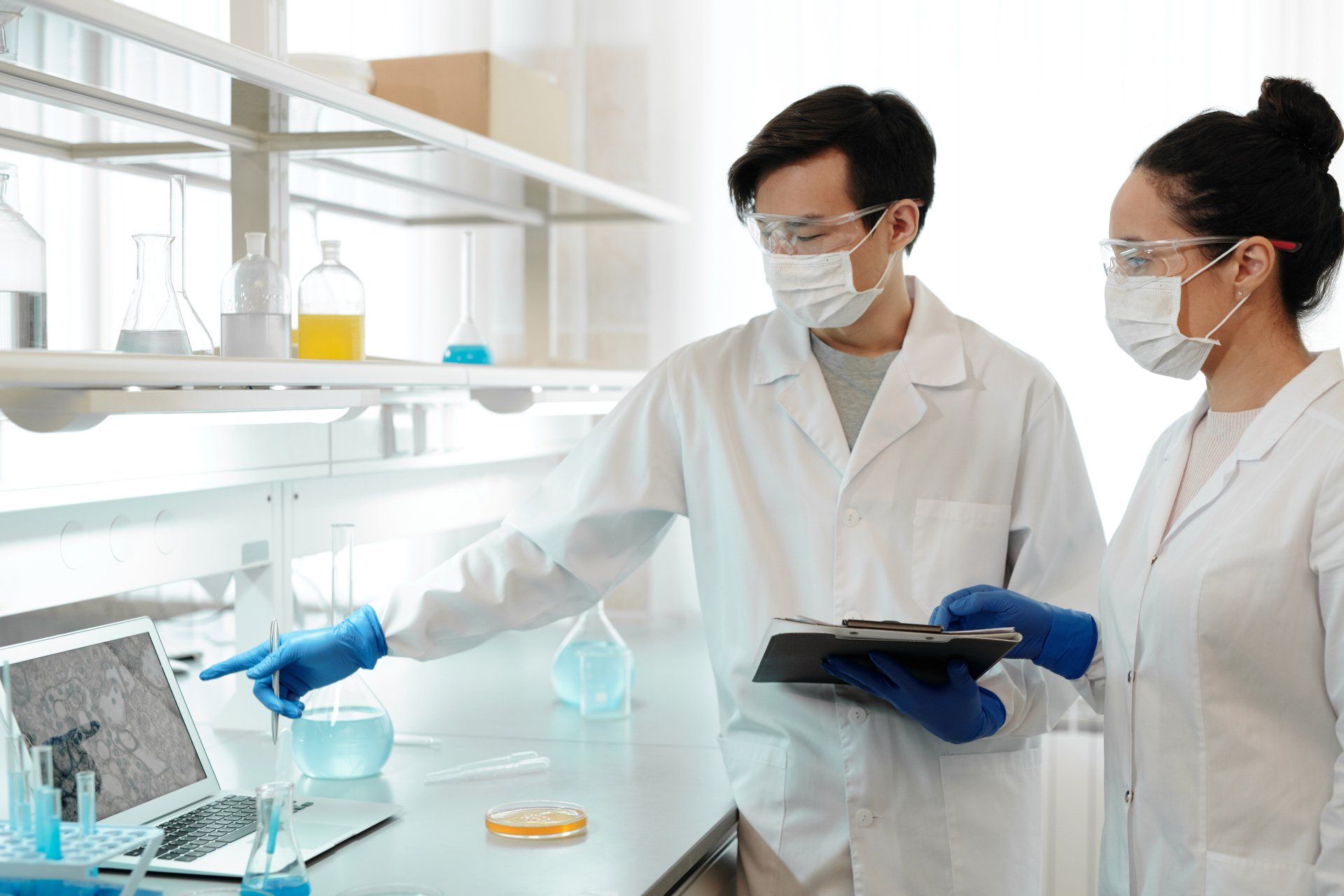
What is lyophilization? This complex process leverages key scientific principles and leading technologies to produce medications ready for transportation and storage. Vaccines, antibodies, and proteins degrade with other methods, making lyophilization critical for many modern treatments.
The utility and popularity of freeze drying is evident in the global freeze drying equipment market, which is estimated to reach $3.5 billion in 2030, up from $1.75 billion in 2022.
Freezing drying pharmaceuticals is an exciting and crucial process. So, keep reading to learn everything you need to know about this central process — and what the future may hold.
Interested in learning about freeze drying? Learn the latest lyophilization technology in our course:
Lyophilization Technology - Application of Scientific Principles
Introduction to Pharmaceutical Freeze Drying
Lyophilization, or freeze drying, is a critical process in the pharmaceutical industry. Freeze drying involves freezing a substance while reducing the surrounding pressure, allowing the frozen water to sublime directly from the solid to the water vapor or gas phase.
This time-tested technique is vital for applications in which sensitive biological materials must be preserved, such as vaccines or antibiotics, which may degrade in liquid form. Lyophilization goes straight from solid to gas, bypassing the potentially detrimental liquid phase.
The Importance of Freeze Drying Pharmaceuticals
Why is this process so vital to pharmaceuticals? Lyophilization drugs are crucial for maintaining efficacy for many types of medication, while also extending shelf life without compromising quality or integrity.
Freeze drying also reduces the weight of the final product by removing water, making storage and transportation more efficient. Pharmaceuticals also become more resistant to temperature changes during shipping and storage.
Brief History of Lyophilization Technology
Freeze drying pharmaceuticals began in World War II and were used to preserve penicillin and blood plasma. Lyophilization was a critical breakthrough as it allowed for longer-term storage and overseas transportation of vital supplies.
The technique proved its utility during wartime, and since then, the lyophilization technology has significantly evolved and has become more widely used for a range of pharmaceuticals, especially antibiotics or vaccines, that need the most extended shelf life possible.
The lyophilisation process has recently enabled enhanced automation, quality control, and scalability — making it a critical tool in producing and distributing pharmaceuticals.
The Process of Freeze Drying
The lyophilization process in the pharmaceutical industry plays a vital role in modern pharmaceutical manufacturing and transportation.
Let’s discuss the process of freeze drying, but be aware processes can vary based on specific needs and chosen pharmaceutical formulations. The overall steps in the lyophilization process are:
- Formulation and pre-freezing: The process begins by choosing the correct formulation and pre-freezing techniques for the specific pharmaceutical. The chosen liquid formulation and pre-freezing practices affect the size and shape of larger ice crystals, which later impacts the drying phases.
- Freezing: The pharmaceutical is brought well below freezing to convert all water into ice. The freezing pattern must be done per the chosen formulation.
- Primary drying phase (sublimation): Next, the pressure is lowered, and heat is applied, which causes the ice to sublimate directly to gas. Primary drying removes roughly 95% water from the product, which must be done carefully to ensure the drug's integrity.
- Secondary drying phase (absorption): The last step focuses on removing the remaining bonded water molecules from the product by increasing the temperature. This stage strives to achieve the ideal moisture content while ensuring the stability and preservation of the lyophilized drugs.
Careful monitoring, temperature control, and pressure control are critical to ensure the stability and quality of the final product.
The lyophilized product is a dry powder, which may be rehydrated when necessary. The product retains its original chemical properties and biological materials found in the pre-frozen material. Lyophilization proteins, antibodies, and other complex molecules benefit significantly from this method, as heat and environmental conditions are otherwise damaging.
Applications of Pharmaceutical Freeze Drying
Freeze drying is used for several pharmaceutical products. Some types of pharmaceuticals that leverage free drying include:
- Vaccines and antibodies that improve longevity and storage, especially when maintaining cold temperatures during transportation are challenging.
- Complex proteins, peptides, and other molecules are used throughout many medications but degrade faster when stored in liquid.
- Enzymes and hormones can also degrade in liquid form and are used in a range of treatments.
- Active pharmaceutical ingredients (APIs) are often biologically derived and freeze dried to remain effective for usage in specific medications.
The freeze drying process improves on other drying methods due to its ability to preserve complex biological products. Lyophilization is a gentle process that minimizes the risk of degradation that can occur with other heat-based methods.
However, one of the limitations of freeze drying is that it’s more time-consuming and energy-intensive — making it more expensive than other methods. Yet, its unique benefits justify the higher costs since it’s able to keep some types of drugs safe and effective during transportation or storage.
Scientific Principles Behind Freeze Drying
Lyophilization is made possible due to physical and chemical scientific principles. We touched on some of these when discussing the process, but let’s dive deeper into the phenomena that make freeze drying possible.
Physical and Chemical Changes
Water in the pharmaceutical product undergoes several changes throughout freeze drying. The liquid water is frozen, then subjected to high pressure, and becomes gas.
Usually, water would have to go through a liquid phase to become a gas — sidestepping this phase preserves the composition and integrity.
Sublimation and Desorption
The direct transition from solid to gas is known as sublimation. Once complete, it’s followed by desorption, a process that removes bound water molecules and further dries the product. Knowing the correct temperatures and pressure levels specific to the chosen formulation is vital to achieving the right results.
The Application of the Phase Diagram
The phase diagram and related temperature points demonstrate the relationship between temperatures and pressure that must be applied to water. Understanding and applying this data is necessary to manufacture a stable product and void degradation.
Equipment and Technology Used in Freeze Drying
Specialized equipment and technologies are what make freeze drying possible. Let’s explore some of the tools necessary for effective freeze drying:
- Freeze dryers: Several types of freeze dryers are available depending on the needs of the manufacturing, including industrial-scale, laboratory, and benchtop models. These different types use similar technologies but vary in scale and use case:
- Industry-scale models are leveraged for mass production.
- Laboratory models are necessary for research and development.
- Benchtop models are used during small-scale experimentation.
- Vacuum and temperature control systems: This equipment is critical for the sublimation and desorption processes. These systems allow for precise control over the pressure and temperature within the freeze dryer to move through each phase.
- Lyophilization trays and condensers: Specialized trays hold the product and are placed within the freeze dryers. These trays are designed to withstand freezing and heating and help provide the necessary environment for sublimation and desorption. Condensers are also located in the freeze dryer and capture the vaporized water, enabling the low pressures necessary for the process.
All of these components work together to create stable and efficient creation of lyophilized products. Each of them is purpose-built to aid in stable and effective workflows.
Challenges and Considerations in Freeze Drying
Freeze drying is not without its unique challenges that need to be understood and addressed. A few of the key challenges include:
- Heterogeneity and collapse: A significant challenge with lyophilization is effectively managing the heterogeneity of the product; otherwise, heterogeneity can result in uneven drying and collapse. This results when some areas of the batch dry improperly, and the pharmaceutical materials lose structure. Addressing this challenge depends on precise control of freeze-drying parameters by understanding the materials' thermal properties.
- Preventing oxidation and moisture absorption: The quality of product can be significantly compromised during transportation or storage without an effective moisture absorption process. This risk can be mitigated by moisture-resistant packaging and possibly adding antioxidants to the formulation.
Stability testing and formulation:
Testing the final product is a critical element of the entire process. Testing involves understanding the stability and shelf life of the freeze dried product. Efficacy should also be evaluated at specific intervals to understand when the product is expired.
Future Advancements and Trends in Pharmaceutical Freeze Drying
- Automation and precision process control: Automation is an in-motion trend that we expect to become more advanced and useful to provide the precision necessary in freeze drying. Ideally, automated systems will be able to monitor critical parameters in real-time and make changes as necessary.
- Lyophilization analytics: Developing tools that provide more detailed analytics about the entire process will be a valuable addition to maximizing value and decreasing energy usage.
Advanced freeze dryer designs: Freeze dryers are undergoing constant improvements and becoming more sophisticated with each new generation. The core goal is to improve condenser efficiency, performance, and reduce cycle times.
Freeze Drying is a Core Pharmaceutical Process
Stay updated on the latest developments in the field with CfPIE. We offer continued education or initial training for you or your workforce to learn the latest technologies and processes in the pharmaceutical industry.
Looking for additional training? Learn more about our programs to learn critical skills for the pharmaceutical and biotech industry.
Blog Categories
Stay Informed