Best Practices for Effective CMC Strategies in Drug Development
Bringing a new drug to market requires a well-planned approach to Chemistry, Manufacturing, and Controls (CMC). A good strategy helps streamline processes, align teams, and ensure drug safety and effectiveness.
Want to avoid delays, cut costs, and boost quality? Keep reading for key strategies on CMC drug development.
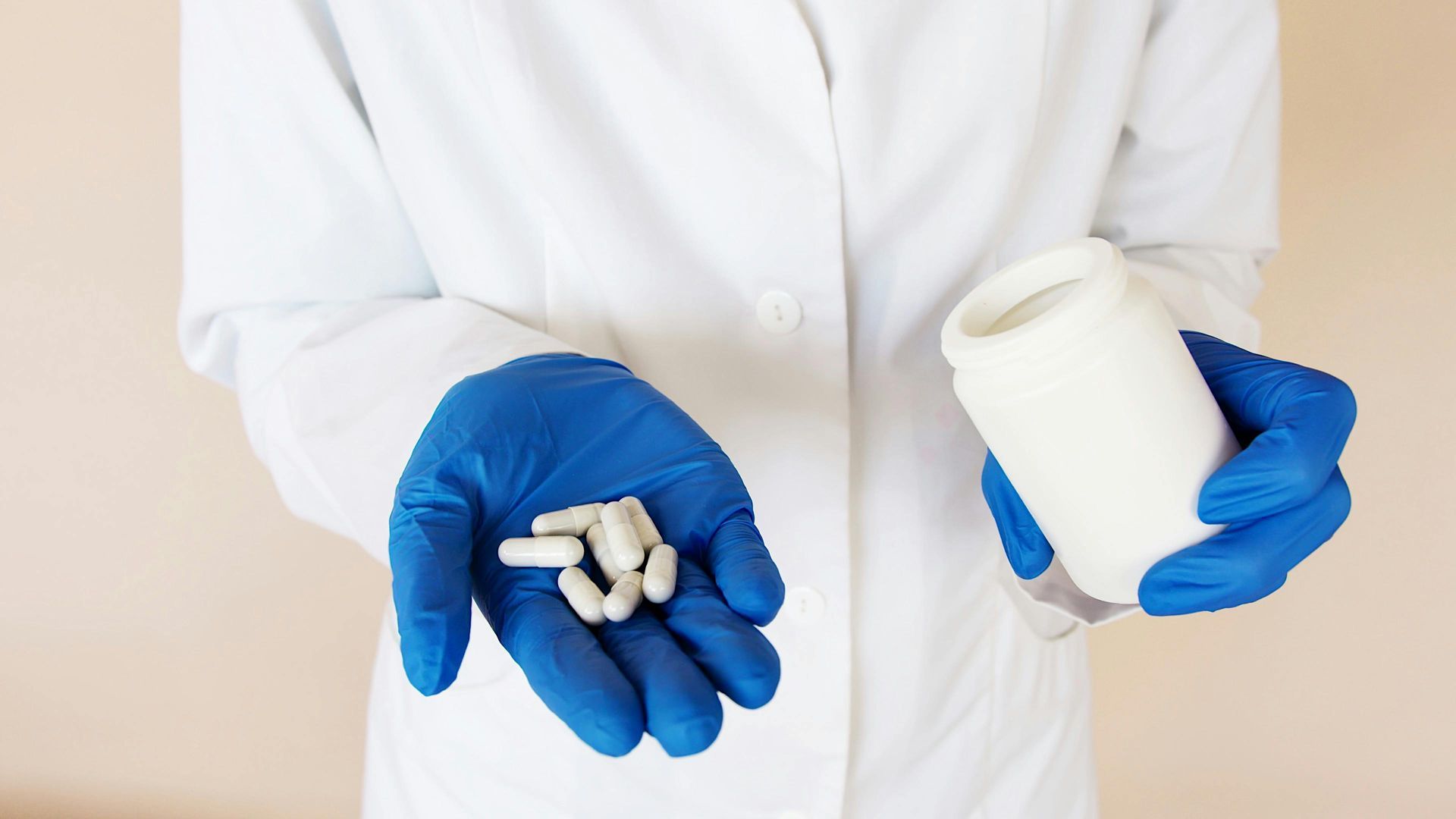
Process Optimization
A strong drug development CMC strategy starts with fine-tuning manufacturing for maximum efficiency and consistency.
Making Manufacturing Smoother
The way a drug is made affects everything, from costs to timelines. Cutting waste, improving consistency, and eliminating bottlenecks can make a big difference. Here’s how:
- Automation: Speeds up production and reduces human errors
- Predictive maintenance: Prevents breakdowns and downtime
- Real-time monitoring: Catches problems before they become bigger issues
- Standardized workflows: Keep every batch consistent and compliant
Advanced Analytical Techniques
Advanced tools like HPLC, mass spectrometry, and spectroscopy give precise data on a drug’s composition, stability, and purity. Catching impurities early helps avoid costly regulatory setbacks.
Planning for Growth from the Start
Scaling up means making more without costly rework. Engineers must consider raw materials, equipment limits, and production costs early for a seamless transition from small batches to full-scale manufacturing.
Risk Management
Spot problems before they start. Here are some key threats to watch for:
- Raw material variability: Supplier differences can throw off formulations.
- Equipment failures: Breakdowns slow production and drive up costs.
- Regulatory missteps: Rules change, and missing updates can stall approvals.
- Stability issues: Environmental shifts can impact drug quality.
Stay ahead of setbacks with safeguards:
- Double-check quality: Extra quality control can catch issues before they escalate
- Secure backup suppliers: Avoid bottlenecks with reliable alternatives
- Plan for disruptions: Have contingency strategies in place to keep production moving
Build Quality into Every Step
Quality by Design (QbD) shifts the focus from testing products after production to ensuring quality from the start. Companies gain greater control and consistency by understanding how formulation and process variables affect the final drug. Instead of relying on inspections to catch defects, QbD integrates quality at every stage of development and manufacturing.
Designing Robust Processes
A well-designed process begins with identifying critical quality attributes (CQAs) and critical process parameters (CPPs). Defining these early ensures the final product remains consistent and meets regulatory standards. Advanced tools like statistical modeling, process analytical technology (PAT), and real-time monitoring help detect variations before they become problems, reinforcing high manufacturing standards.
Continuous Improvement
Continuous improvement keeps processes efficient and compliant long after initial production. A culture of learning, routine data analysis, and feedback loops drive ongoing enhancements. Post-market surveillance helps products keep their intended quality, allowing companies to adapt to new challenges while staying ahead in regulatory compliance.
Strength in Collaboration
When chemists, engineers, regulatory specialists, and manufacturing teams collaborate, they bridge gaps between development and production. Early alignment can prevent expensive modifications, ensure smooth scaling, improve efficiency, and speed up time to market.
Effective Communication
Clear communication ensures critical information reaches the right people at the right time. Establishing standardized documentation practices, holding regular meetings, and sharing real-time data improves coordination and ensures clear communication.
Leverage Technology
Using technology in CMC helps companies work faster, stay efficient, and meet regulations more easily. Machine learning predicts issues before they happen, automation reduces errors and speeds up production, and cloud-based systems make tracking data and submitting regulatory documents easier.
Mastering CMC for a Competitive Edge
Effective CMC drug development strategies integrate process optimization, risk management, regulatory compliance, and cross-functional collaboration. Companies that prioritize quality, embrace technology, and streamline communication will see an improvement in both efficiency and risk reduction.
CfPIE provides the training and expertise to navigate these complexities through courses like
CMC Regulatory Compliance Strategy for Cell & Gene Therapy Medicines and
CMC Regulatory Compliance Strategy for Recombinant Proteins, Monoclonal Antibodies, & Biosimilars.
Sign Up Today
Blog Categories
Stay Informed