How GMP Best Practices Ensure Quality Control in the Pharmaceutical Industry
The pharmaceutical industry is highly regulated due to its effect on patient outcomes. Medications must maintain a consistent level of quality and effectiveness; otherwise, patients pay the price.
The specific regulations vary between jurisdictions, but abiding by Good Manufacturing Practices (GMP) creates the baseline for safe and effective pharmaceutical manufacturing. Drug manufacturers can make specific changes to abide by applicable regulatory requirements from there.
GMP best practices focus largely on quality assurance and quality control (QA/QC), which is a set of processes and inspections, all designed to ensure drugs, biologics and medical devices meet established guidelines and effectiveness.
How exactly does this play out in the pharmaceutical industry? Keep reading to learn more about this crucial topic, including the benefits and challenges of abiding by GMP best practices to ensure quality control.
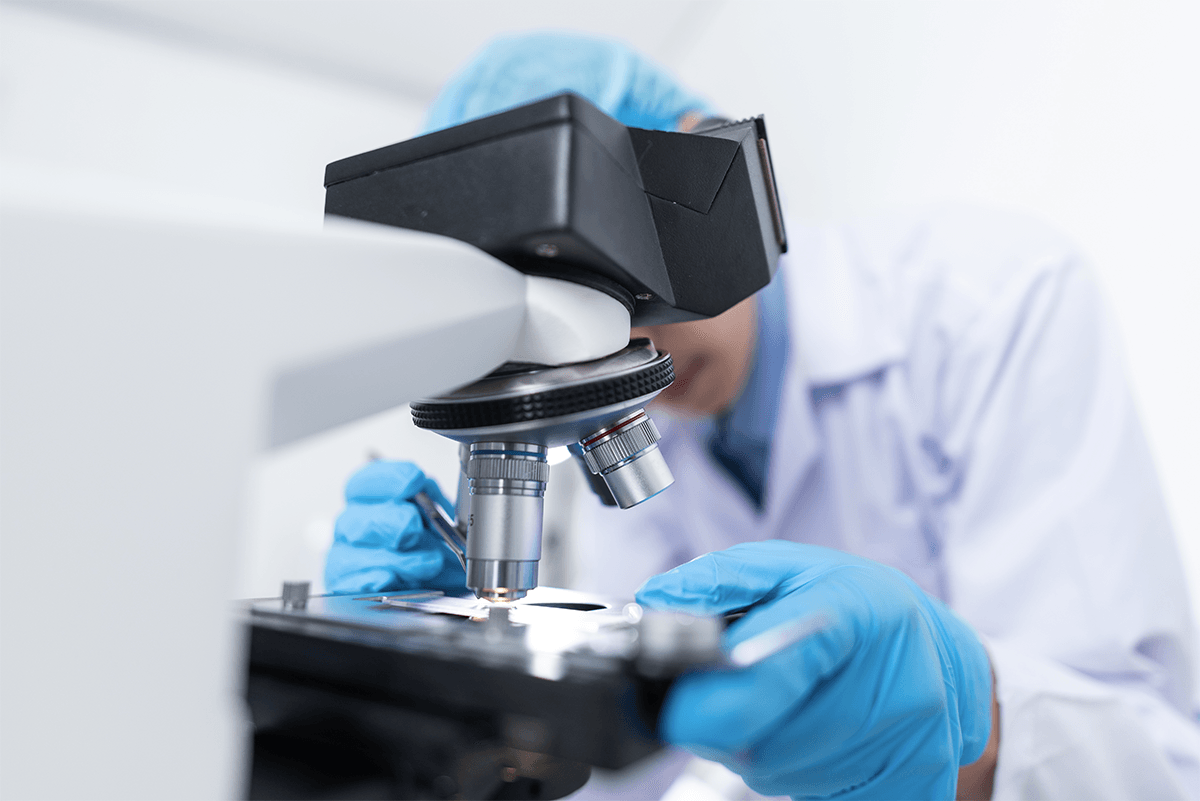
Importance of Quality Assurance and Quality Control in the Pharmaceutical Industry
Quality Assurance and Quality Control (QA/QC) in the pharmaceutical industry is not only about meeting standards — it's a critical component of public health. Over-the-counter and prescription medications directly affect millions of individuals' health and well-being daily.
Inconsistent quality or the presence of impurities can lead to adverse reactions, diminished efficacy, or even harm patients. QA/QC ensures that every batch of a drug on the market is consistent in strength, purity, and effectiveness. Additionally, comprehensive quality control processes can identify potential issues at an early stage, allowing for corrective actions to be taken before products reach consumers.
QA/QC serves as a protective measure and a cornerstone for maintaining the credibility and reputation of pharmaceutical companies in an industry where trust is of the utmost importance.
What is Quality Control in Manufacturing?
QA/QC ensures that medicine reaching consumers meets the highest quality standards. Quality control encompasses testing products against predefined standards, documenting processes, calibrating instruments, and monitoring the entire manufacturing environment.
Regulatory authorities set these standards to ensure medicinal products are safe and effective. Compliance with all applicable regulations is crucial, and non-compliance can lead to potential recalls or legal repercussions.
Overview of GMP Guidelines and Regulations
QA/QC in the pharmaceutical industry is primarily based on Good Manufacturing Practice (GMP) guidelines and regulations. This framework sets the standards for pharmaceutical manufacturing and quality control.
GMP isn’t exclusive to the pharmaceutical industry — it’s a widely used framework for many industries. Regarding pharmaceutical manufacturing, GMP encompasses various aspects of production, from the starting materials, premises, and equipment to staff training and personal hygiene.
These guidelines and regulations aim to ensure medications are consistently produced and meet the standards related to their intended use. Beyond the manufacturing process, GMP also focuses on comprehensive testing methods for final product release.
Adherence to GMP guidelines is not optional — it's a mandatory aspect of pharmaceutical production, and failure to comply can result in significant penalties, recalls, or even business closures. The only exception is specific jurisdictions, but drugs manufactured in these areas typically cannot be imported into other regions that require GMP.
Critical Components of GMP Best Practices in QA/QC
GMP guidelines strive to guarantee that products have consistent quality in every batch, regardless of the manufacturer. Everyone involved in production and quality management needs to be trained on GMP validation best practices to prevent affecting patient care and incurring steep fines or penalties.
Let’s review some of the vital components of GMP that strive to maintain consistent quality and effectiveness, such as:
- Documentation and record-keeping: Comprehensive documentation and meticulous record-keeping are foundational GMP best practices. Good documentation practices ensure traceability, provide evidence of compliance, and enable a thorough review of production processes to facilitate any corrective actions.
- Training and qualification of personnel: The proficiency of the personnel directly impacts the quality of the pharmaceutical product. As such, rigorous quality assurance training and regular assessments are vital to ensure staff are equipped with the latest knowledge and skills to uphold GMP standards.
- Facility and equipment maintenance: A well-maintained facility and equipment are essential to prevent contamination and errors. Frequent inspections, cleaning, and calibrations ensure the production environment meets regulatory standards.
- Raw material control and testing: Ensuring the quality and consistency of raw materials is of the utmost importance. Thorough testing and robust control measures ensure that only materials meeting predefined quality criteria are used in production.
- Process validation and monitoring: To guarantee consistent product quality, it's necessary to validate and continuously monitor all processes. Validation ensures that the manufacturing remains within defined parameters and that any deviations can be promptly addressed.
- Packaging and labeling control: Correct packaging and accurate labeling are crucial to product integrity and patient safety. Strict controls make sure all primary packaging materials conform to established specifications, that products are packaged to prevent contamination, and that labels provide accurate, precise information.
- Product testing and release: All products must pass rigorous testing to meet all safety and efficacy standards before reaching the market. GMP quality assurance makes sure only batches that pass these stringent tests are approved for release.
- Complaint handling and product recall procedures: Manufacturers need an effective system for addressing customer complaints and potential product recalls. These procedures should be well-documented and ensure any issues are handled properly to protect public health and maintain the credibility of the pharmaceutical manufacturer.
Benefits of Implementing GMP Best Practices in QA/QC
Adopting best practices in GMP audits and quality control is a significant step forward for pharmaceutical manufacturers. Integrating GMP best practices into an organization’s quality control testing framework and manufacturing processes has several significant benefits.
Let’s break down some of these benefits manufacturers may experience when adhering to GMP best practices.
Consistent Product Quality
GMP prioritizes strict standards to ensure every product batch is consistent. This consistency means that each medication will provide the same therapeutic effect regardless of when or where it's produced.
As a result, healthcare professionals can prescribe these medicines with the certainty that patients will receive the intended benefits without unexpected variations in dosage strength or effectiveness.
Increased Patient Safety
The strict GMP procedures are designed to reduce the risks associated with pharmaceutical manufacturing, such as reducing the chance of errors, contaminations, and inconsistencies. These risks may lead to adverse reactions or lack the necessary effectiveness if left unchecked.
Abiding by GMP best practices ensures the medicine patients depend on is more likely to be safe, pure, and free from harmful impurities.
Better Economic and Operational Efficiency
GMP isn't just about quality — it's also about efficiency. Implementing these best practices can streamline production processes, reduce waste, minimize downtime, and create faster turnaround times. The economic benefits start to add up when manufacturers reduce the likelihood of costly recalls, reworks, or waste.
Reinforced Public Trust
Reputation is everything in the pharmaceutical industry. Medicines are directly linked to personal well-being, and consumers need to trust their products.
Abiding by GMP best practices and standards builds a company's reputation for producing high-quality, reliable medications. Additionally, consistent quality assurance builds public confidence and increases brand loyalty and trust.
Regulatory Compliance
Pharmaceutical regulations are intricate and never stand still. GMP best practices help manufacturers remain agile and compliant while also adapting to new regulatory requirements as they emerge. Manufacturers will also prevent possible legal issues and ensure products can seamlessly enter and remain in markets with rigorous regulatory standards.
Challenges and Potential Solutions in Implementing GMP Best Practices
GMP best practices provide many benefits, but implementing these standards and practices can be challenging. Some of these challenges and possible solutions include the following:
- Insufficient training and skill development: Employees may not have adequate knowledge of current GMP standards. This can lead to unintentional non-compliance, jeopardizing product quality and safety. Regular and comprehensive training programs should be implemented. Additionally, these programs should be updated as regulations change.
- Outdated infrastructure and equipment: Older manufacturing facilities or machinery might not meet the stringent requirements of modern GMP. Pharmaceutical companies should invest in modern, efficient, and GMP-compliant equipment that ensures regulatory compliance and can enhance production efficiency.
- Inconsistent documentation practices: Document errors or omissions can have severe consequences for product traceability and accountability. These issues are also a significant obstacle in demonstrating GMP compliance during audits. Fortunately, digital systems and software tools can automate many aspects of documentation, reducing the potential for human error.
- Evolving regulatory standards: GMP and other applicable regulations are not set in stone. Regulations are updated to reflect the most current understanding of safety and efficacy. To address this challenge, companies need to establish dedicated teams or hire experts to monitor and interpret regulatory changes. This proactive approach can also minimize the disruption of adapting to new standards.
- Supply chain inconsistencies: The quality and consistency of raw materials sourced from suppliers can vary, creating unwanted variability in the final product. Implementing rigorous vetting processes is crucial, and quality checks upon receipt of materials can alleviate this challenge.
Importance of GMP Best Practices and Ongoing Training
Following GMP best practices protects the reputation of companies, improves patient care, and fosters trust within the global healthcare community.
However, as the pharmaceutical industry evolves, so do the challenges related to compliance and GMP best practices designed to address these challenges. Fortunately, these hurdles can be overcome with proactive solutions like continuous training, investment in infrastructure, and embracing new technologies.
CfPIE is an industry-recognized provider of training and certification courses throughout pharmaceutical manufacturing. Our courses prepare and certify specialists to help keep their employer’s complaint while ensuring effective patient care.
Is it time for your quality assurance specialists to learn the latest GMP best practices and regulations?
Learn more about our QA certification course to discover how we can help.
Blog Categories
Stay Informed